Novarc’s coil welding robot (SWR) is designed to automate pipe welding and works alongside a human welder to increase productivity. Images: Novarc
Today’s production environment can be challenging. A lack of skilled welders makes it difficult to meet customers’ labor and technical demands.
For those working in tube and pipe manufacturing, conventional industrial robots have not always been accessible for pipe welding applications.
To address these challenges, Novarc engineers developed the Spool Welding Robot (SWR), a collaborative welding robot designed to help manufacturers automate the pipe spool welding process and provide precision and agility to ensure welds are completed correctly. carried out.
In recent years, Novarc has been working on artificial intelligence (AI) technology to take SWR to the next level. In July this year, it launched its NovEye Autonomy Gen 2, a real-time vision processing system that continuously improves weld quality based on data collection and model improvement to fully automate the pipe welding process. Canadian Fabricating & Welding spoke with Novarc co-founder and CEO Soroush Karimzadeh about this new technology.
CFW: What is the SWR and how does it work?
Karimzadeh: Our coil welding robot is a welding robot designed to automate pipe welding. It works together with a human welder to improve productivity.
However, the NovEye Autonomy release will expand the capabilities of the SWR, allowing it to be set up by a welder or operator, who can then walk away after the initial setup.
The NovEye Autonomy technology is powered by AI that we have developed over many years.
Our company is a pioneer in the field of autonomous welding. We’ve been able to leverage the data we’ve collected from a fleet of robots we’ve developed and deployed over the years.
With this date, we have developed computer vision AI models that can analyze the weld pool and respond to different changes or variations in the pipe, just like a human welder would. Using the SWR with the NovEye Autonomy gives human welders the freedom to perform various shop tasks that cannot be automated or require manpower.
CFW: What market conditions or trends make this type of technology necessary in the workplace?
Karimzadeh: The biggest trend is the acute shortage of human welders, which has been present in the manufacturing industry for some time. According to recent estimates, the US economy is missing approximately 250,000 human welders. This comes against a backdrop of rising demand, especially with recent U.S. legislation appropriating more infrastructure spending, leading to more welding and fabrication projects. This demand only further exposes the skills gap and the recognition that welding automation can help mitigate labor shortages.
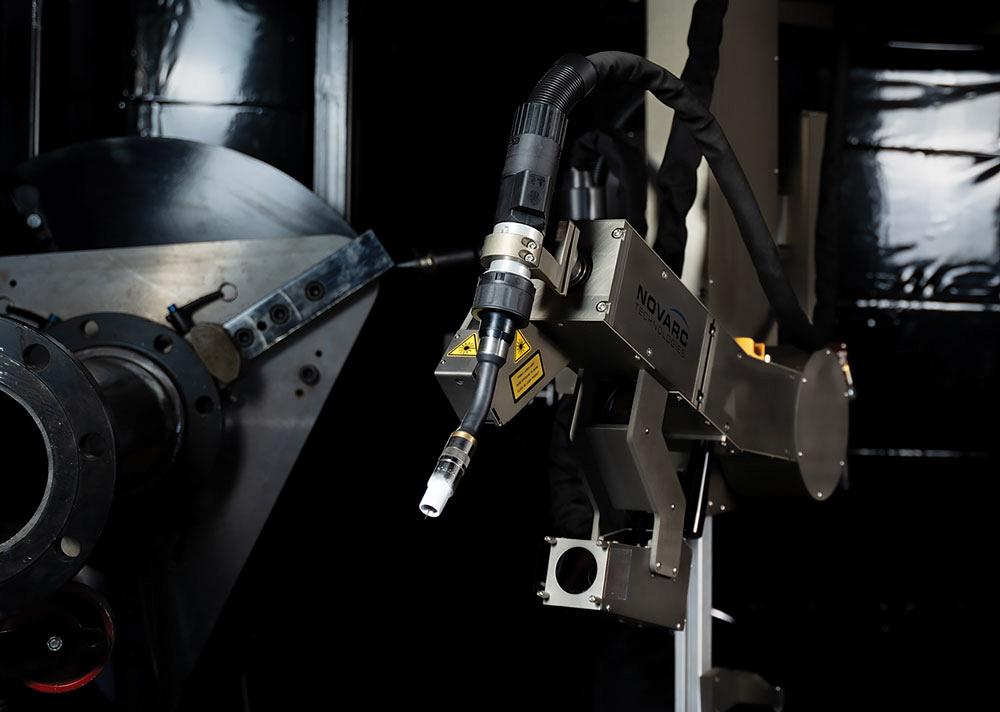
According to Soroush Karimzadeh, the pipe repair rate among North American shops is around 3 to 5 percent. The SWR reduces this to less than 1 percent by producing consistent, high-quality welds every time.
Pipe welding is carried out in almost all industrial sectors to manufacture pipe coils. These components are used, for example, in the oil and energy industries such as LNG plants, refineries and carbon capture plants. Pipe welding is used in construction, especially pipes associated with water and wastewater. It is also carried out in the construction of high-rise buildings, stadiums and even the retrofitting of ships. The applications are broad and very diverse.
Pipe welding as an application itself can be very difficult. The average application range for shops in North America is between 50 and 70 inches. diam. More importantly, the repair rate for these stores is approximately 3 to 5 percent. With the coil welding robot, which automates pipe welding, we can reduce that repair rate to less than 1 percent. We do this by producing consistent, high-quality welded connections. And of course, with NovEye Autonomy, operators can now set up the line, press the machine’s start button, and the rest is taken care of, performing as perfectly as a human could, if not better.
NovEye Autonomy is unique because for the first time, welding automation has comparable intelligence, in terms of welding capabilities, to what human welders could do before.
CFW: How does NovEye Autonomy improve welding quality and performance?
Karimzadeh: With NovEye Autonomy, a human operator is no longer required to perform the SWR. For example, if a manufacturer currently produces 6,000 welds per year with a repair rate of 2 to 3 percent, you are likely spending about $180,000 per year on repairs. By reducing the repair rate to less than 1 percent, manufacturers can integrate these costs back into the bottom line and support the company to move to the next phase of growth.
NovEye Autonomy is an AI machine learning real-time vision processing system that continuously improves welding based on data collection and model improvement. It gets smarter as it continuously improves thanks to a library of terabyte-scale welding videos, ensuring precision and reliability.
The software is embedded in the cobot’s control system and controls the weld pool in the same way as a human welder would, allowing the robot to take over more repetitive welds that can be delegated to the robot. The autonomous welding process enables uninterrupted welding thanks to the multi-layer and multi-layer autonomous welding system, which is able to address real-world pipe fitting inconsistencies such as Hi-Lo and varying root gaps. NovEye Autonomy can instantly detect and adjust welding parameters to maintain weld integrity.
CFW: What do stores need to know to make sure this is a good fit for them?
Karimzadeh: This product really makes sense for manufacturers whose core business is welding different sizes and thicknesses of pipe. Novarc also wants to work with stores that could benefit from deploying such automation in their operations. We are looking for workshops that not only want to increase their productivity while reducing repair costs, but also want to attract a new generation of welders.
Today’s welders may not have the same skills or interest as welders of the past. However, they may be attracted to working with a robot or cobot, working with AI and working in a more innovative way. That is, we are looking for forward-thinking shops that plan to recruit talent but will benefit from SWR deployment while increasing productivity and reducing repair rates.
For new NovEye Autonomy customers, no additional hardware is required. The SWR is equipped with enough computing power, backed by NVIDIA, to run highly advanced, large machine learning models that can handle this load in real time and autonomously take on the task of pipe quality.
In terms of the degree of automation and ease of use, it is no different from robots introduced in the welding industry.
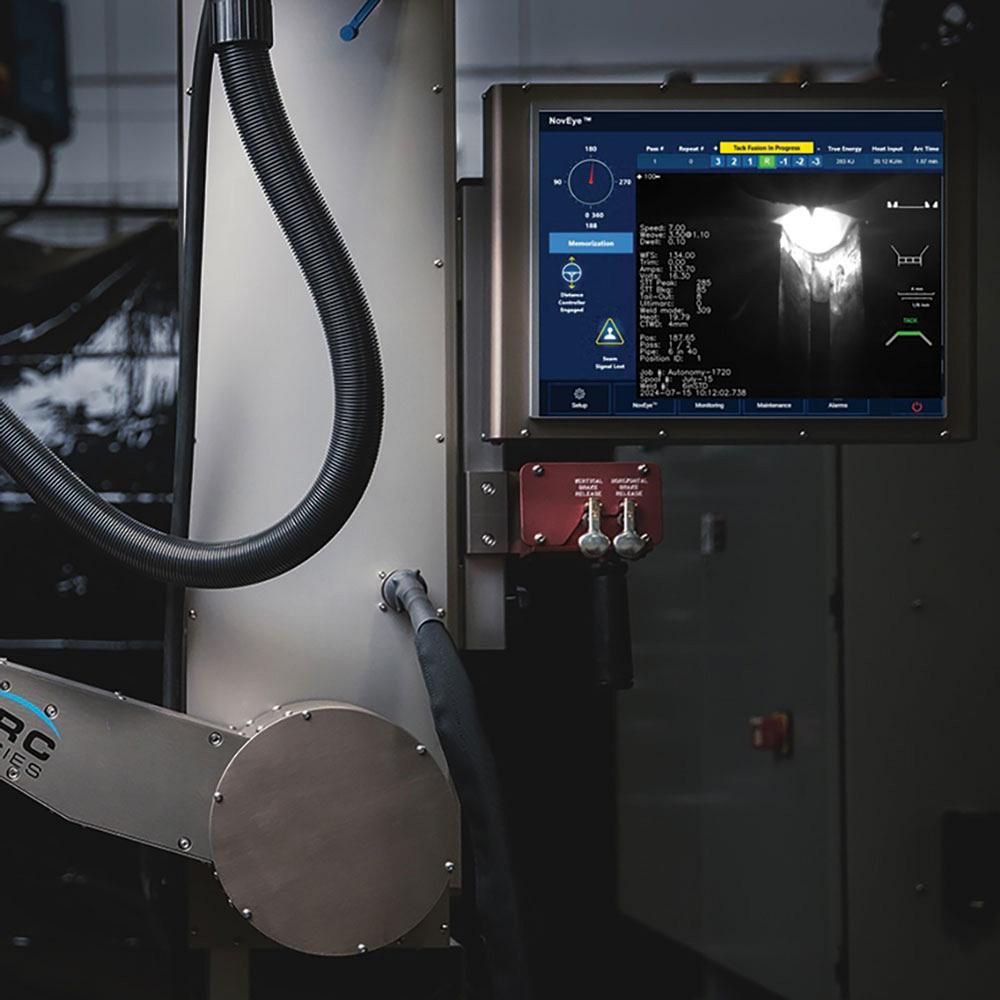
The NovEye Autonomy release extends the capabilities of Novarc’s SWR, allowing it to be set up by a welder or operator, who can then walk away after the initial setup.
A coil welding robot is very easy to use. There is no robot programming involved. The extra level of autonomy obviously makes it even easier to deploy. This is mainly because the level of training and skills required of SWR operators has been significantly reduced. For the most part, automation is seen as difficult to implement, but the SWR, with the added autonomy, we have made very simple. Of course, this is based on the success of more than a hundred implementations over the years.
SWR and NovEye Autonomy are specifically designed for pipe spool production, a high-mix, low-volume production. But that said, in the near future we plan to develop AI models that support a wider range of welding environments, including different materials and different geometries. Our primary goal today is to ensure that our customers will be successful with their NovEye Autonomy, but we are also working on a future generation of AI models that can do much more than just pipe welding, using the latest and greatest in the field of AI innovation and its application to our welding automation solutions.
Based on our experience, we have developed change management and project management tools that can help someone new to welding automation succeed, not only in installation and training, but also in using it effectively in production. We have a customer success team that can work with customers to ensure the robots go into production as quickly as possible. That’s an important part of what it can help with.
NovArc Technologies, www.novarctech.com